روش مورد استفاده جهت استخراج مس به طبیعت و ترکیبات مس موجود در سنگ معدن بستگی دارد. به طور کلی سه روش اصلی برای استخراج مس وجود دارد:
۱- روش ذوب مستقیم:
این روش برای استخراج مس از سنگ های اکسیدی پرعیار بکار می رود(درصد مس در کلوخه هابایستی ازبیشتر۹۰% باشد).این روش قدیمی بوده و امروزه به علت کمیاب شدن سنگ اکسیدی پرعیار،از صنعت خارج شده است.
اساس این روش حذف کامل گوگرد از سنگ معدن و احیاء بعدی آن توسط عوامل احیاء کننده مانند کربن ویا گاز co قرارر دارد.این روش به دلایل تلفات زیاد مس در سرباره و مصرف سوخت و انرژی بالا، غیر اقتصادی می باشد.
۲- روش تغلیظ کردن( تهیه مات):
این روش برای ترکیبات گوگردی مس یا مس طبیعی با عیار کم بکار رفته می شمد .ابتدا سنگ های معدنی گوگرددار در کوره های ذوب به مات مس که مجموعه ای از سولفوره های مس و آهن است،تبدیل شده وسپس توسط یک کنورتر،مس خام از آن بدست می آید که بعداً مورد توجه قرار می گیرد.این روش دارای مزایای زیر می باشد:
وجود عناصر گرمازا در مات،که کنورتر را بی نیاز از سوخت های خارجی می کند.
-درجه خلوص مس خام (نسبت به روش احیاء)
-عدم احتیاج به تشویه و یا در صورت لزوم یک تشویه جزئی
۳- روش شستشوی اسیدی (لیچینگ):
این روش در مورد سنگ های اکسیدی و به خصوص کربنات ها به کار می رود.سنگ های مورد مصرف در این روش می تواند کم عیار باشد، همچنین ممکن است که سنگ های گوگردی را نیز مورد عمل تشویه قرار داده و سپس در یک حلال حل کرده و مس آن را به روش های مختلف جدا کرد.
این روش از نظر بهداشت محیط زیست نسبت به طریقه ی احیاء و تشکیل مات دارای مزایای بیشتری است.در هر حال هیدرو متالوژی مس و تهیه مس از طریق تشکیل مات دو روش اصلی متالوژی مس می باشند.
لیچینگ عبارتست از تجزیه کانی با روش موجود در سنگ معدن یا کنسانتره که عموماً توسط یک حلال انجام می شود.گاهی اوقات عملیات به صورت تجزیه مواد ثانوی مو جود در مواد قراضه ،پس مانده و باطله نیز گسترش می یابد.به طوری که لیچینگ برای کلوخه های سنگ یا مواد معدنی با ارزش که مقدار آن در پس مانده های سنگ معدنی موجود هستند به کار می رود.
لیچینگ هیپ و دامپ
لیچینگ هیپ و دامپ در اصل شبیه به هم می باشد وتفاوت در نوع معدن و مقدار فلز موجود در آن می باشد.در لیچینگ هیپ سنگ های معدنی کم عیار بوده وسنگ ها را در ابتدا خرد کرده و سایزهای یکسان در می آیند و به صورت یک بستری به ارتفاع ۳ متر در می آورند که وزن این بستر ها چند صد تن می باشد.بستر را بر روی لایه پلیمری غیر قابل نفوذ در مقابل محلول رقیق اسیدی بر سطح زمین می سازند.در این لایه حفره هایی تعبیه شده که محلول خروجی را به سمت یک کانال هدایت می کنند.اسیداشی هم از بالای بستر انجام می شود.این نوع لیچینگ برای معادن زیر زمینی به کار می رود وسنکگ معدن را بعد از استخراج به سطح زمین می آورند و بستر در سطح زمین ساخته می شود.
لیچینگ دامپ در مقیاس بزرگتری انجام می شود و عموماً در معادن روباز انجام می گیرد.سنگ ها را بعد از خرد شدن به صورت بستری آماده می سازند، سنگ ها در اندازه هنای مختلف موجود هستند و دانه بندی نمی شوند. از نظر زمانی مدت زمان عملیات لیچینگ در دامپ مدت زمان بیشتری طول می کشد وگاهی مدت چند سال به طول می انجامد،در حالی که در هیپ زمان فرایند کمتر می باشد.
دسته بندی فرآیند لیچینگ
فرایند لیچینگ به دو فرایند اکسیدی و غیر اکسیدی تقسیم می شود:
فرایند لیچینگ غیر اکسیدی
تر کیبات مس کر بنات دار همچون ما لاکیت و آزوریت یون مس یا یون سولفات موجود در اسید سولفوریک رقیق واکنش می دهد و سولفات مس به وجود می آیدودیاگرام استخراج مس در فرآیند غیر اکسیدی را نشان می دهد.
فرآیند لیچینگ اکسیدی
در این فرایند دو محلول فرو شوینده باز،یک عامل اکسید کننده موجود باشد تا بتواند ترکیبات سولفیدی مس را در اثر اکسید کردن به صورت تر کیبات سولفاتی در آورد تا بتواند با اسید واکنش دهد.
روش های مختلف لیچینگ
درجا دامپ و هیپ می باشند،ولی کانی های مس با همه روش های فوق قابل بازیابی هستند.هزینه عملیاتی و سرمایه ای لیچینگ درجا ،دامپ و هیپ نسبتاً کم بوده بنابراین برای سنگ های معدنی با عیار کم مناسب می باشند.ولی لیچینگ همزنی و حوضچه ای هزینه دبالاتری نسبت به درجا،دامپ و هیپ دارند. در نتیجه برای سنگ های معدنی با عیار بالا و کنسانتره مناسب می باشند.
بررسی روش های لیچینگ:
لیچینگ حو ضچه ای
این روش یکی از روش های قدیمی لیچینگ آمونیاکی کنسانتره های اکسیدی حاصل ازروش ثقلی و لیچینگ آمونیاکی سنگ معدن های مس آزاد بکار برده می شود.این روش معمو لاً برای سنگ ها ی اکسیدی مس با عیار بالا(۱-۲%مس) به کار برده می شود. ابعاد مواد معدنی مناسب برای این روش ۴/۳ تا ۸/۴ اینچ می باشد.در این روش از مخزن های به عمق ۲۰فوت و ابعاد ۶۰ فوت که دارای یک کف سو راخ است استفاده می شود. مواد به داختل حوضچه ها ریخته می شود و با توجه به حجم مخزن که ۱۲۰۰۰تن جامد است زمان یک یسیکل کامل در این روش ۱۰۰-۲۰۰ ساعت متغیر است و باز یابی در این روش تا ۹۶% می رسد این روش دارای یک سرس مزایا است از جمله بازیابی بالا تو لید محصول باردار(PLS) با عیار بالا حذف فیلتر و تیکنر است.
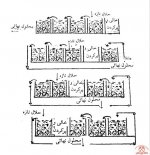
۱- ذوب مستقیم (direct smelting) یا روش احیاء
۲- تغلیظ کردن (concentration) یا روش تهیه مات
۳- شستشوی اسیدی (leaching) یا روش هیدرومتالوژی
۱- روش ذوب مستقیم:
این روش برای استخراج مس از سنگ های اکسیدی پرعیار بکار می رود(درصد مس در کلوخه هابایستی ازبیشتر۹۰% باشد).این روش قدیمی بوده و امروزه به علت کمیاب شدن سنگ اکسیدی پرعیار،از صنعت خارج شده است.
اساس این روش حذف کامل گوگرد از سنگ معدن و احیاء بعدی آن توسط عوامل احیاء کننده مانند کربن ویا گاز co قرارر دارد.این روش به دلایل تلفات زیاد مس در سرباره و مصرف سوخت و انرژی بالا، غیر اقتصادی می باشد.
۲- روش تغلیظ کردن( تهیه مات):
این روش برای ترکیبات گوگردی مس یا مس طبیعی با عیار کم بکار رفته می شمد .ابتدا سنگ های معدنی گوگرددار در کوره های ذوب به مات مس که مجموعه ای از سولفوره های مس و آهن است،تبدیل شده وسپس توسط یک کنورتر،مس خام از آن بدست می آید که بعداً مورد توجه قرار می گیرد.این روش دارای مزایای زیر می باشد:
وجود عناصر گرمازا در مات،که کنورتر را بی نیاز از سوخت های خارجی می کند.
-درجه خلوص مس خام (نسبت به روش احیاء)
-عدم احتیاج به تشویه و یا در صورت لزوم یک تشویه جزئی
۳- روش شستشوی اسیدی (لیچینگ):
این روش در مورد سنگ های اکسیدی و به خصوص کربنات ها به کار می رود.سنگ های مورد مصرف در این روش می تواند کم عیار باشد، همچنین ممکن است که سنگ های گوگردی را نیز مورد عمل تشویه قرار داده و سپس در یک حلال حل کرده و مس آن را به روش های مختلف جدا کرد.
این روش از نظر بهداشت محیط زیست نسبت به طریقه ی احیاء و تشکیل مات دارای مزایای بیشتری است.در هر حال هیدرو متالوژی مس و تهیه مس از طریق تشکیل مات دو روش اصلی متالوژی مس می باشند.
لیچینگ عبارتست از تجزیه کانی با روش موجود در سنگ معدن یا کنسانتره که عموماً توسط یک حلال انجام می شود.گاهی اوقات عملیات به صورت تجزیه مواد ثانوی مو جود در مواد قراضه ،پس مانده و باطله نیز گسترش می یابد.به طوری که لیچینگ برای کلوخه های سنگ یا مواد معدنی با ارزش که مقدار آن در پس مانده های سنگ معدنی موجود هستند به کار می رود.
لیچینگ هیپ و دامپ
لیچینگ هیپ و دامپ در اصل شبیه به هم می باشد وتفاوت در نوع معدن و مقدار فلز موجود در آن می باشد.در لیچینگ هیپ سنگ های معدنی کم عیار بوده وسنگ ها را در ابتدا خرد کرده و سایزهای یکسان در می آیند و به صورت یک بستری به ارتفاع ۳ متر در می آورند که وزن این بستر ها چند صد تن می باشد.بستر را بر روی لایه پلیمری غیر قابل نفوذ در مقابل محلول رقیق اسیدی بر سطح زمین می سازند.در این لایه حفره هایی تعبیه شده که محلول خروجی را به سمت یک کانال هدایت می کنند.اسیداشی هم از بالای بستر انجام می شود.این نوع لیچینگ برای معادن زیر زمینی به کار می رود وسنکگ معدن را بعد از استخراج به سطح زمین می آورند و بستر در سطح زمین ساخته می شود.
لیچینگ دامپ در مقیاس بزرگتری انجام می شود و عموماً در معادن روباز انجام می گیرد.سنگ ها را بعد از خرد شدن به صورت بستری آماده می سازند، سنگ ها در اندازه هنای مختلف موجود هستند و دانه بندی نمی شوند. از نظر زمانی مدت زمان عملیات لیچینگ در دامپ مدت زمان بیشتری طول می کشد وگاهی مدت چند سال به طول می انجامد،در حالی که در هیپ زمان فرایند کمتر می باشد.
دسته بندی فرآیند لیچینگ
فرایند لیچینگ به دو فرایند اکسیدی و غیر اکسیدی تقسیم می شود:
فرایند لیچینگ غیر اکسیدی
تر کیبات مس کر بنات دار همچون ما لاکیت و آزوریت یون مس یا یون سولفات موجود در اسید سولفوریک رقیق واکنش می دهد و سولفات مس به وجود می آیدودیاگرام استخراج مس در فرآیند غیر اکسیدی را نشان می دهد.
فرآیند لیچینگ اکسیدی
در این فرایند دو محلول فرو شوینده باز،یک عامل اکسید کننده موجود باشد تا بتواند ترکیبات سولفیدی مس را در اثر اکسید کردن به صورت تر کیبات سولفاتی در آورد تا بتواند با اسید واکنش دهد.
روش های مختلف لیچینگ
- لیچینگ حوضچه ای
- لیچینگ همزنی
- لیچینگ برجا
- دامپ و هیپ لیچینگ
درجا دامپ و هیپ می باشند،ولی کانی های مس با همه روش های فوق قابل بازیابی هستند.هزینه عملیاتی و سرمایه ای لیچینگ درجا ،دامپ و هیپ نسبتاً کم بوده بنابراین برای سنگ های معدنی با عیار کم مناسب می باشند.ولی لیچینگ همزنی و حوضچه ای هزینه دبالاتری نسبت به درجا،دامپ و هیپ دارند. در نتیجه برای سنگ های معدنی با عیار بالا و کنسانتره مناسب می باشند.
بررسی روش های لیچینگ:
لیچینگ حو ضچه ای
این روش یکی از روش های قدیمی لیچینگ آمونیاکی کنسانتره های اکسیدی حاصل ازروش ثقلی و لیچینگ آمونیاکی سنگ معدن های مس آزاد بکار برده می شود.این روش معمو لاً برای سنگ ها ی اکسیدی مس با عیار بالا(۱-۲%مس) به کار برده می شود. ابعاد مواد معدنی مناسب برای این روش ۴/۳ تا ۸/۴ اینچ می باشد.در این روش از مخزن های به عمق ۲۰فوت و ابعاد ۶۰ فوت که دارای یک کف سو راخ است استفاده می شود. مواد به داختل حوضچه ها ریخته می شود و با توجه به حجم مخزن که ۱۲۰۰۰تن جامد است زمان یک یسیکل کامل در این روش ۱۰۰-۲۰۰ ساعت متغیر است و باز یابی در این روش تا ۹۶% می رسد این روش دارای یک سرس مزایا است از جمله بازیابی بالا تو لید محصول باردار(PLS) با عیار بالا حذف فیلتر و تیکنر است.
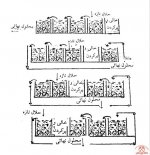
شکل(۱-۲):لیچینگ به روش حوضچه ای