این آسیاب معمولا به شکل استوانه است که در آن حجم معینی گلوله فولادی یا سرامیکی با سایز مشخص وجود دارد. کل حجم این استوانه توسط موتور و گیربکس بسیار قدرتمند حول یک محور به چرخش در میآید و در اثر غلطیدن و برخورد این گلولهها به روی مواد اولیه آنها را به صورت پودر تبدیل میکند.
از این نوع آسیاب در تولید پودرهای میکرونیزه(خشک و مایع) با مشهای مختلف جهت استفاده در صنایعی مانند رنگسازی- کاشیسازی- داروسازی و غیره استفاده میگردد. از محاسن بزرگ این آسیاب تولید پودر میکرونیزه با مش یکدست میباشد. این مزیت دستگاه باعث شده در صنایعی مانند سیمان، داروسازی، رنگسازی و لعاب کاری بیشترین و بهترین استفاده را داشته باشد.
آسیاب گلولهای یا بالمیل در دو نوع خشک ( دارای ورودی و خروجی همزمان ) و نوع مایع ( ظرف بسته ) ساخته میشود .
در نمونه خشک مواد اولیه از یک سمت وارد میشود و پس از فرایند آسیاب شدن و به مش مورد نظر رسیدن، محصول از سمت دیگر خارج میشود. ظرفیت آن بر مبنای مش متغییر است و برای مثال یک دستگاه با ظرفیت ۵۰۰ کیلو در ساعت با مش ۲۰۰، تولیدی به ظرفیت ۳۰ کیلو در ساعت مش ۱۵۰۰ خواهد داشت.
نوع دیگر این آسیاب یا نوع مایع آن که بیشتر شبیه گوی ساخته میشود دارای یک ورودی و خروجی میباشد و غیر از آن مواد به بیرون راه ندارد. مصرف این دستگاه در مواردی است که بخواهند مایعی ( امولسیون ) با مش یک دست بدست آورد. مانند لعاب سرامیک. از این دستگاه کمتر جهت مواد خشک استفاده میشود زیرا در آسیاب نوع خشک محصول اغلب توسط مکنده تفکیک کننده ( سپراتور ) جدا میشود و از آسیاب خارج میگردد اما در این نوع آسیاب مواد اولیه را وارد دستگاه کرده درب آنرا میبندند و پس از مدت زمان معین درب آنرا باز و مواد را خارج میکنند.
در زمانهایی که ظرفیت تولید در پودر خشک نیز کم باشد و دقت در سایز محصول زیاد مورد اهمیت نباشد نیز از شکل استوانهای آن استفاده میگردد.
آسیاب بال میل در کارخانههای سیمان، سرب، مس، روی و . . . داروسازی، اسید و امثال آن کاربرد فراوانی دارد. استفاده از گلولههای سرامیکی و زره داخلی سرامیکی در صنایع داروسازی و رنگ سازی و اسید و … میباشد. چون در این صنایع معمولا وجود فلزات ناشی از استهلاک مورد قبول نمیباشد و محصول را خراب مینماید.
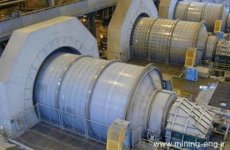
فرآیند آسیا
برای خرد کردن بیشتر محصول بهدست آمده در مسیرهای سنگشکنی، از انواع آسیاها استفاده میشود. آسیاها ممکن است به طریقه خشک یا تر کار کنند که انتخاب آن بستگی به نوع کانه و مراحل بعدی عملیات دارد.
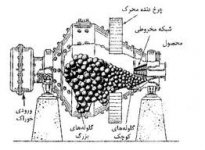
بهعنوان مثال اکثر کانههای سولفوره به طریقه تر، طی یک یا چند مرحله آسیا میشوند تا به درجه آزادی مناسب برسند. کانههای آهن را ممکن است بسته به نوع عملیات پرعیار کردن، به طریقه تر یا خشک آسیا کرد. در مورد کانههای غیر فلزی، مسیرهای آسیا کردن بسیار متفاوت هستند. به عنوان مثال در مورد باریت اکثرا آسیا کردن و پرعیار کردن به طریقه تر است و نظر به این که محصول پرعیار شده آن، در صنایع مربوطه باید دانهبندی کوچکتری داشته باشد، ابتدا خشک میشود و مراحل بعدی آسیا کردن به طریقه خشک انجام میشود.
از انواع آسیاهای متداول در صنعتی میتوان به آسیاهای میلهای، آسیاهای گلولهای، آسیاهای لولهای، آسیاهای خودشکن، آسیاهای نیمه خودشکن، آسیاهای قائم، آسیاهای غلتکی، آسیاهای دمشی و… اشاره کرد.
از این نوع آسیاب در تولید پودرهای میکرونیزه(خشک و مایع) با مشهای مختلف جهت استفاده در صنایعی مانند رنگسازی- کاشیسازی- داروسازی و غیره استفاده میگردد. از محاسن بزرگ این آسیاب تولید پودر میکرونیزه با مش یکدست میباشد. این مزیت دستگاه باعث شده در صنایعی مانند سیمان، داروسازی، رنگسازی و لعاب کاری بیشترین و بهترین استفاده را داشته باشد.
آسیاب گلولهای یا بالمیل در دو نوع خشک ( دارای ورودی و خروجی همزمان ) و نوع مایع ( ظرف بسته ) ساخته میشود .
در نمونه خشک مواد اولیه از یک سمت وارد میشود و پس از فرایند آسیاب شدن و به مش مورد نظر رسیدن، محصول از سمت دیگر خارج میشود. ظرفیت آن بر مبنای مش متغییر است و برای مثال یک دستگاه با ظرفیت ۵۰۰ کیلو در ساعت با مش ۲۰۰، تولیدی به ظرفیت ۳۰ کیلو در ساعت مش ۱۵۰۰ خواهد داشت.
نوع دیگر این آسیاب یا نوع مایع آن که بیشتر شبیه گوی ساخته میشود دارای یک ورودی و خروجی میباشد و غیر از آن مواد به بیرون راه ندارد. مصرف این دستگاه در مواردی است که بخواهند مایعی ( امولسیون ) با مش یک دست بدست آورد. مانند لعاب سرامیک. از این دستگاه کمتر جهت مواد خشک استفاده میشود زیرا در آسیاب نوع خشک محصول اغلب توسط مکنده تفکیک کننده ( سپراتور ) جدا میشود و از آسیاب خارج میگردد اما در این نوع آسیاب مواد اولیه را وارد دستگاه کرده درب آنرا میبندند و پس از مدت زمان معین درب آنرا باز و مواد را خارج میکنند.
در زمانهایی که ظرفیت تولید در پودر خشک نیز کم باشد و دقت در سایز محصول زیاد مورد اهمیت نباشد نیز از شکل استوانهای آن استفاده میگردد.
آسیاب بال میل در کارخانههای سیمان، سرب، مس، روی و . . . داروسازی، اسید و امثال آن کاربرد فراوانی دارد. استفاده از گلولههای سرامیکی و زره داخلی سرامیکی در صنایع داروسازی و رنگ سازی و اسید و … میباشد. چون در این صنایع معمولا وجود فلزات ناشی از استهلاک مورد قبول نمیباشد و محصول را خراب مینماید.
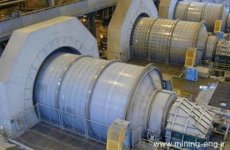
فرآیند آسیا
برای خرد کردن بیشتر محصول بهدست آمده در مسیرهای سنگشکنی، از انواع آسیاها استفاده میشود. آسیاها ممکن است به طریقه خشک یا تر کار کنند که انتخاب آن بستگی به نوع کانه و مراحل بعدی عملیات دارد.
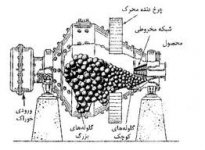
بهعنوان مثال اکثر کانههای سولفوره به طریقه تر، طی یک یا چند مرحله آسیا میشوند تا به درجه آزادی مناسب برسند. کانههای آهن را ممکن است بسته به نوع عملیات پرعیار کردن، به طریقه تر یا خشک آسیا کرد. در مورد کانههای غیر فلزی، مسیرهای آسیا کردن بسیار متفاوت هستند. به عنوان مثال در مورد باریت اکثرا آسیا کردن و پرعیار کردن به طریقه تر است و نظر به این که محصول پرعیار شده آن، در صنایع مربوطه باید دانهبندی کوچکتری داشته باشد، ابتدا خشک میشود و مراحل بعدی آسیا کردن به طریقه خشک انجام میشود.
از انواع آسیاهای متداول در صنعتی میتوان به آسیاهای میلهای، آسیاهای گلولهای، آسیاهای لولهای، آسیاهای خودشکن، آسیاهای نیمه خودشکن، آسیاهای قائم، آسیاهای غلتکی، آسیاهای دمشی و… اشاره کرد.